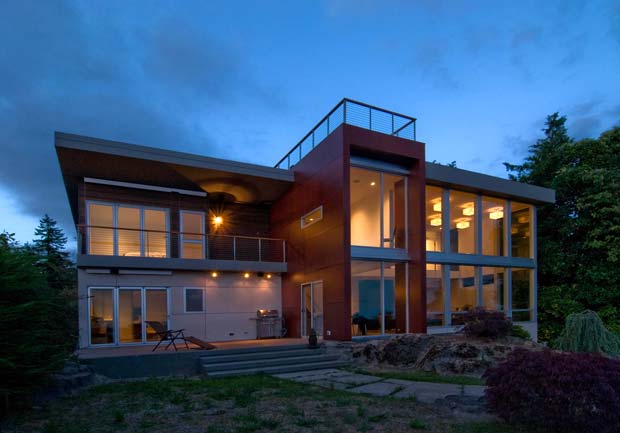
Having just spent four years in a condo without a deck, the importance of nailing one’s deck strategy was clear to me from the start of this project. I wanted decks in as many places as it made sense, in order to take advantage of the property’s great views and outdoor entertaining potential.
There was already a large patio area outside where the old house used to be so that part was easy. Here’s what the patio looks like now:
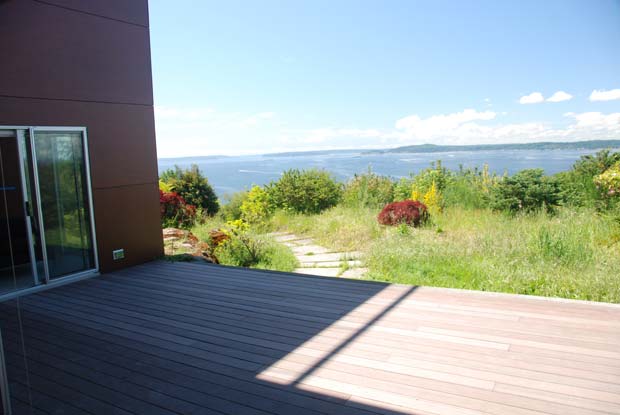
Additionally, the plans called for a master bedroom facing southwest looking over Puget Sound so putting a little reading deck out there was an easy call as well. We ended up making this deck about two feet shallower so we could extend the interior space of the master bedroom out a bit, but it’s still plenty big enough for having a glass of wine or reading a book on. Here’s what it looks like:
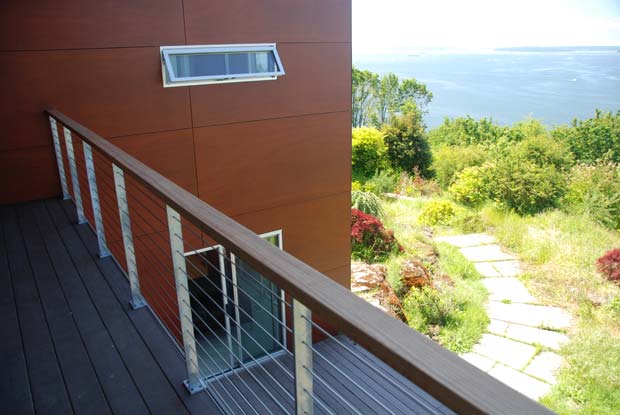
The coup de gras grâce, however, is the rooftop deck. I don’t understand why everybody doesn’t build one of these. Flat roofs with rooftop decks are so much more useful and fun than sloped roofs with, uhhh, shingles. If you have any sort of view whatsoever, you should have a rooftop deck. Here’s how ours ended up:
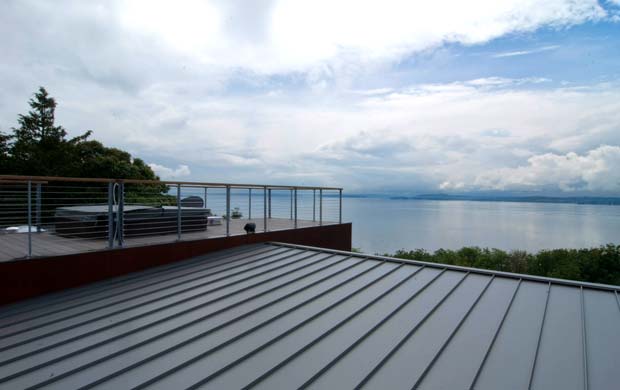
Now on to some particulars…
For the material, we ended up using Trex Brasilia in espresso color. I did a ton of research into decking materials and concluded that there are no panaceas. The only wood that is as durable and trouble-free as I’d like is ipe, but it cannot easily be stained and tends to silver quickly — a look I was not interested in. Concrete pavers are the lowest maintenance option, but they feel tough on the feet and we already have enough concrete around the outside of the house. Composite decking reviews are all over the map with some installations performing well for people and others exhibiting mold and other problems fairly quickly. We ended up going with Trex because it is a brand that’s been around a long time and it looked the least fake to us. So far so good on the Trex.
For railings, we went with ipe for its low maintenance qualities. Since it’s just the railing, we don’t mind the silvering here.
For posts, we went with galvanized steel with steel cables running through them. I’m not a huge fan of how galvanized steel looks and went to great pains to minimize its use throughout the project (particularly on the awning), but considering the low profile of the posts, it was a good low maintenance material to use here.
As mentioned in the hot tub post, we went with a HotSpring Sovereign hot tub for the rooftop deck and couldn’t be happier with it so far. It might be the best feature of the house.
Costs accrued during this stage:
Decking materials (Plywood Supply) | $6,211.00 |
Decking parts and labor (Deerly Construction) | $5,441.00 |
Decking materials (Compton Lumber) | $1,411.00 |
Decking materials (Plywood Supply) | $2,206.00 |
Decking parts and labor (Brett Deerly) | $4,601.00 |
Trex Brasilia decking material (Plywood Supply) | $1,788.00 |
Deck railing (Feeney) | $3,588.00 |
Deck flashing (Precision Fabricators, LLC) | $592.00 |
Guardrail galvanizing (Scott Galvanizing) | $135.00 |
Guardrail fabrication (Twisted Metalworks) | $5,164.00 |